Lafayette Formula Electric Car
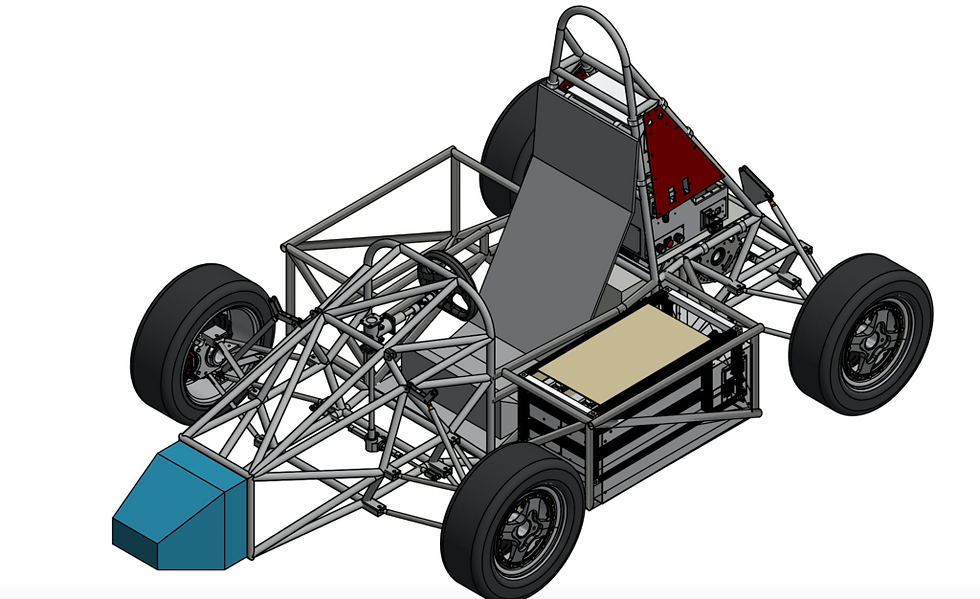


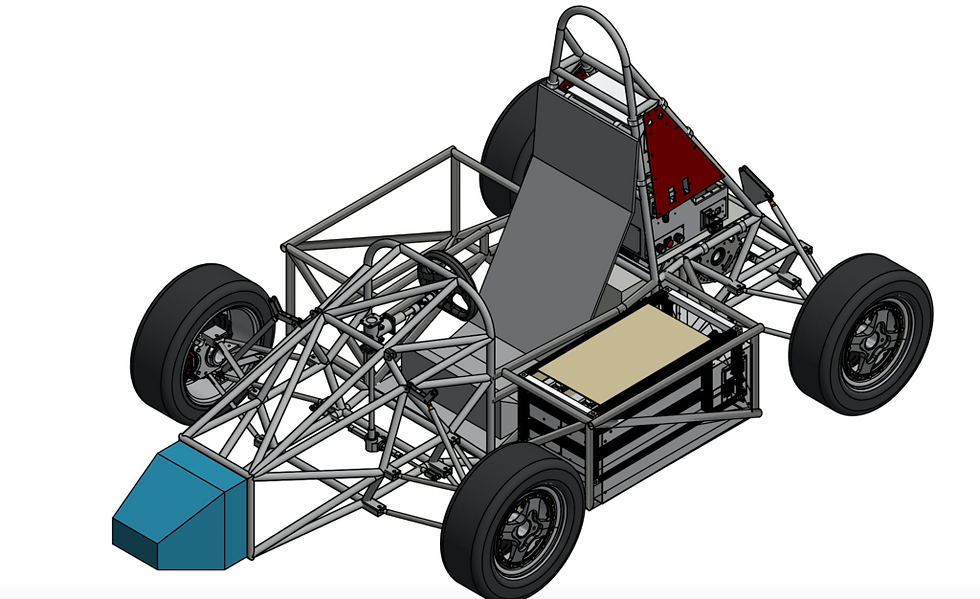
The Lafayette Motorsports Team consists of 22 mechanical and electrical engineering students and professors. In 2018, the team began designing Sparky for the FSAE hybrid competition.
Personally, I was responsible for electrical systems integration, FSAE competition worksheets and forms, classwide presentations, and intercollegiate formula team meetings. Eventually, I was nominated for a leadership position within the team.
​
FSAE rules compliance and safety were considered in all design decisions.
​
Drivetrain Design and Analysis:




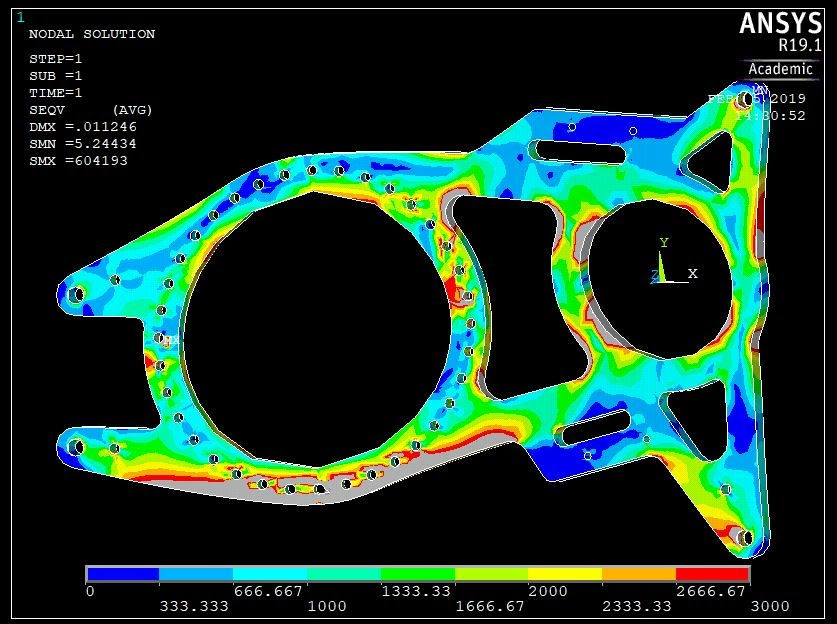


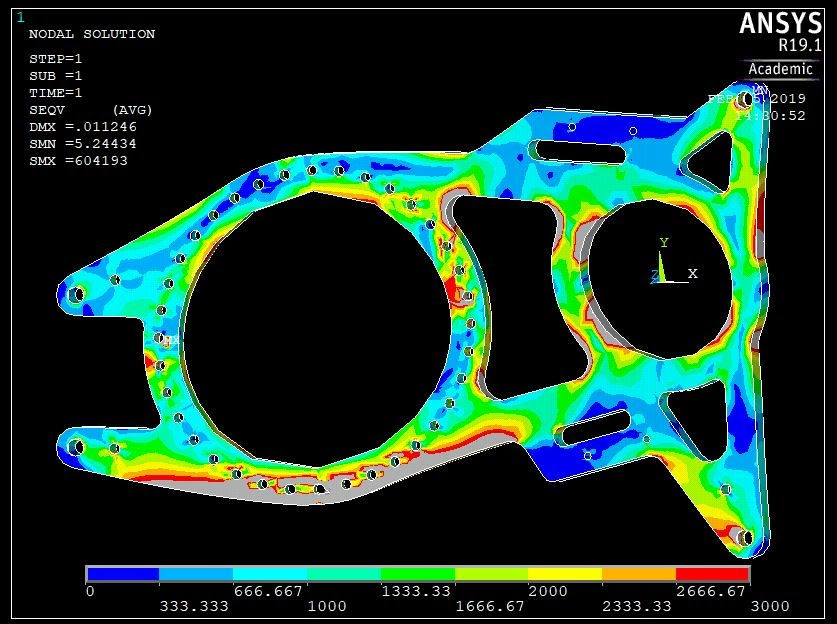
This project consisted of designing a single gear electric drivetrain for the vehicle. I was tasked with selecting a motor, modeling several drivetrain designs, performing FEA analysis, and using MatLab to predict vehicle performance. Once my design was finished, I held several teamwide design reviews and made revisions. Then I generated part drawings and a bill of materials. I assisted with the manufacture, assembly, and installation of the housing, motor, and rear differential.
​
Drivetrain Features:
-
A two-plate design makes the overall system lighter and easier to assemble compared to previous iterations.
-
An eccentric chain tensioner and 2 springloaded rollers provide easy and effective tensioning.
-
The compact design allows for full subsystem assembly before installation.
​
I performed fatigue and crash test analysis using Ansys. Using MatLab, I modeled straight-line acceleration tests to help the team pick the optimal gear ratio.
Dynamometer Test Enclosure
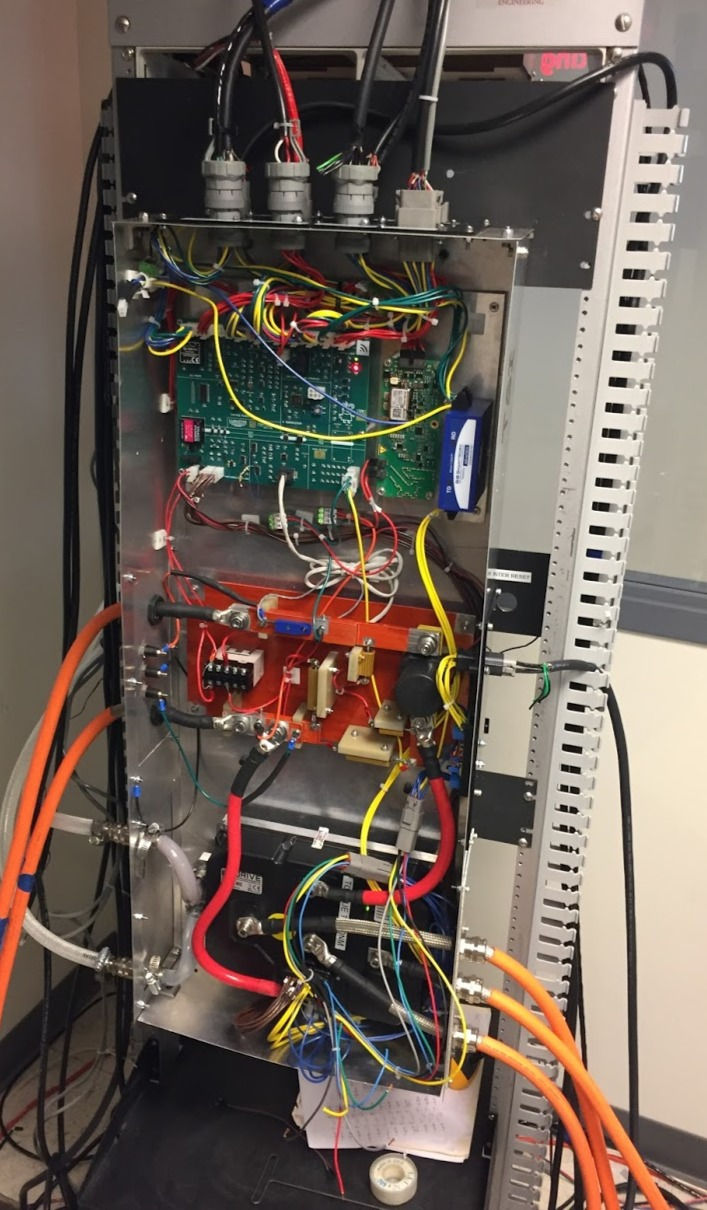


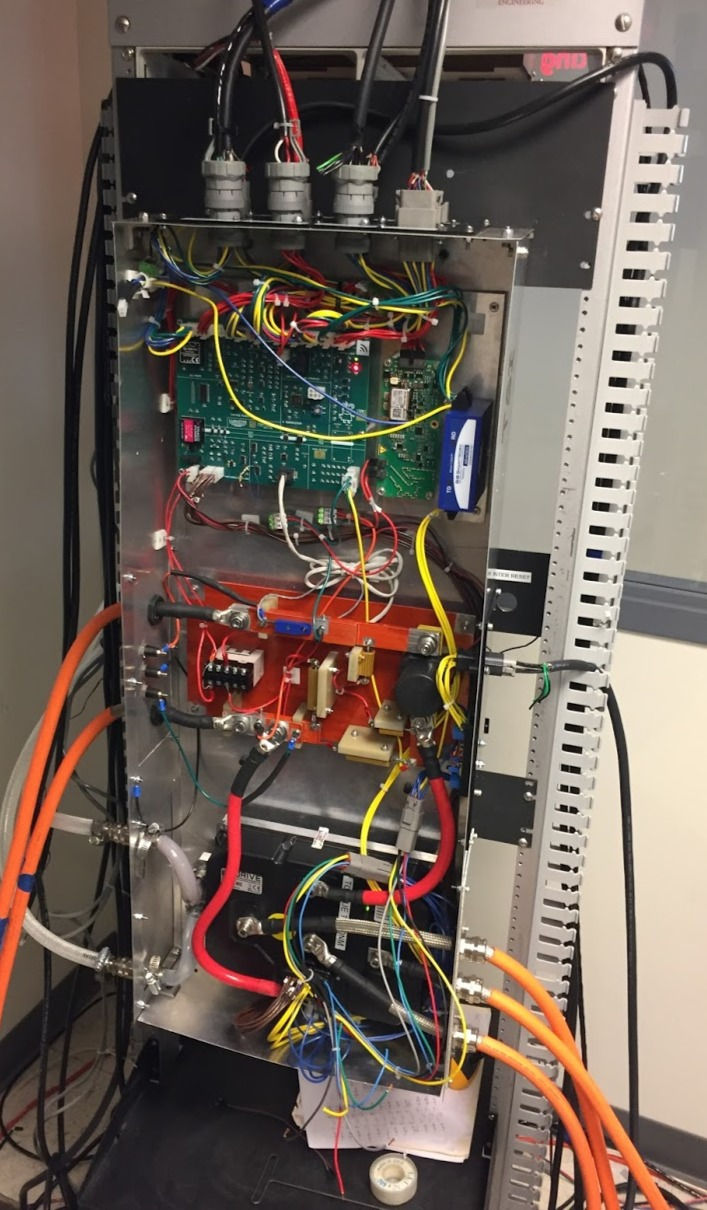
During my 1st year on the team, I volunteered to design a test enclosure for the team's dynamometer. I worked closely with several electrical teams, helping to transform their ideas and hand sketches to CAD. Once a final design was approved I manufactured and assembled the system.
My responsibilities included CAD, several design reviews and revisions, part selection, BOM, and shop drawing generation and assembly.
​
This enclosure contains 3 main subsystems: The tractive system interface at the top, the high-voltage relay board in the middle, and the motor controller at the bottom.
CarMan
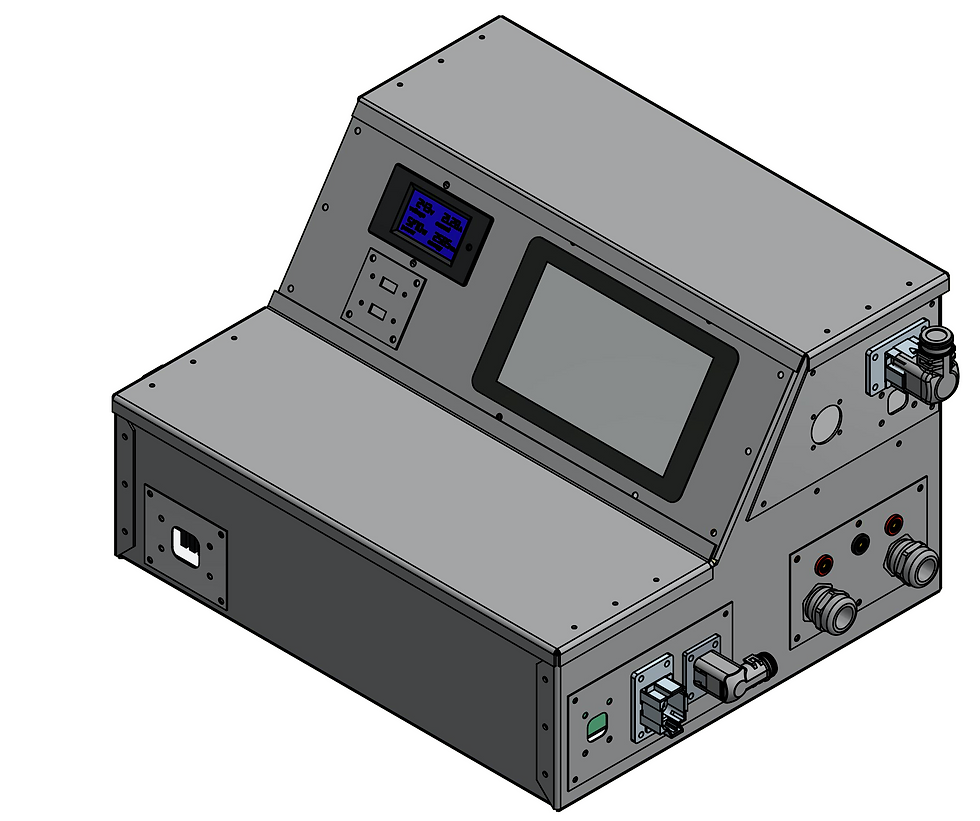
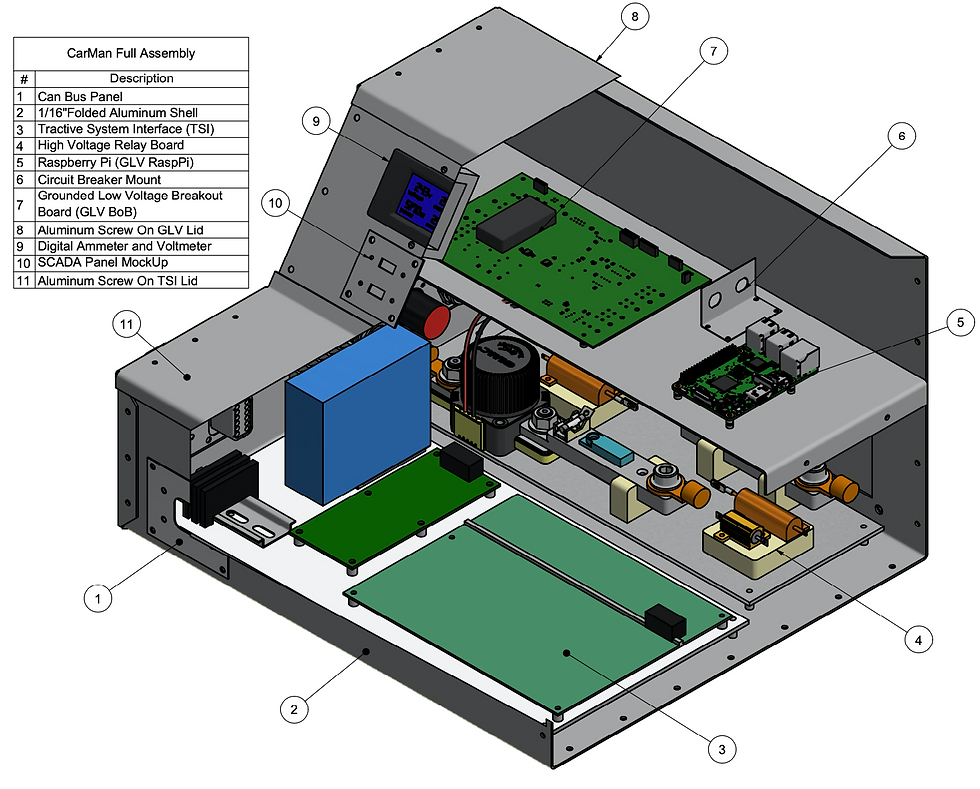
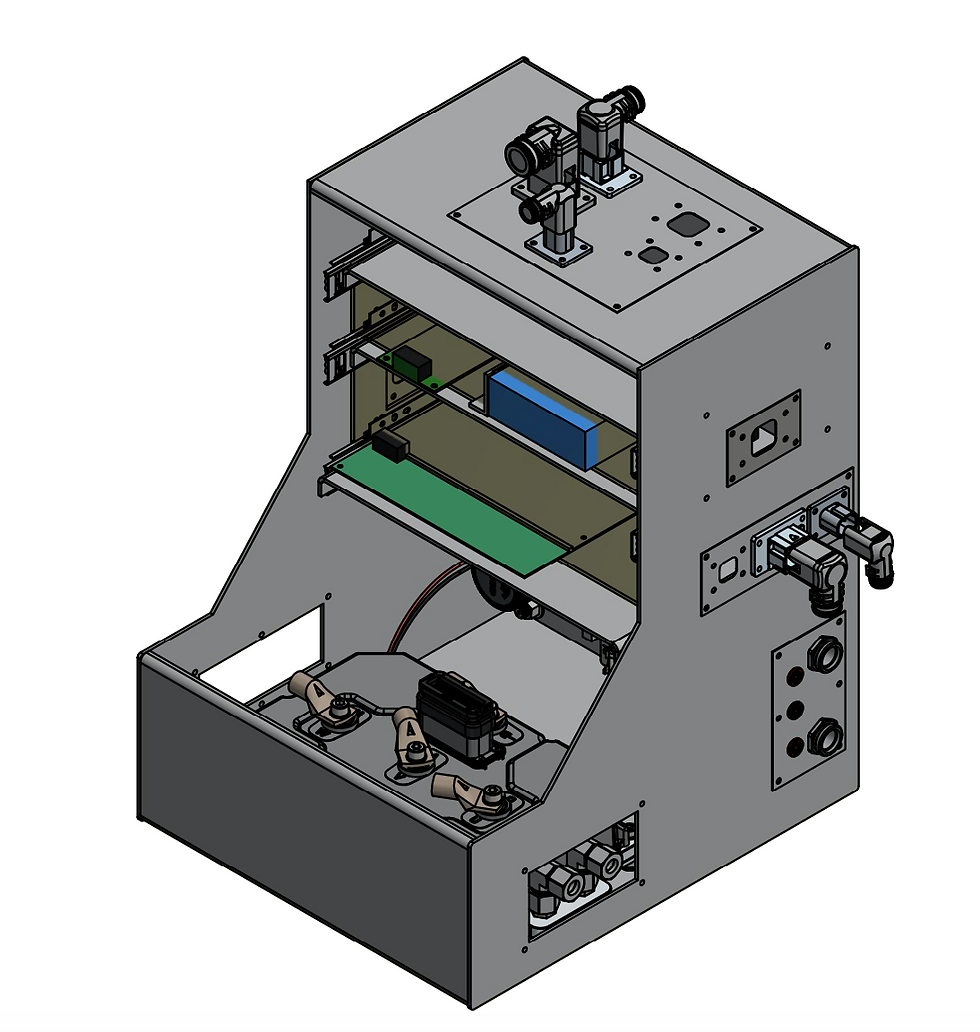
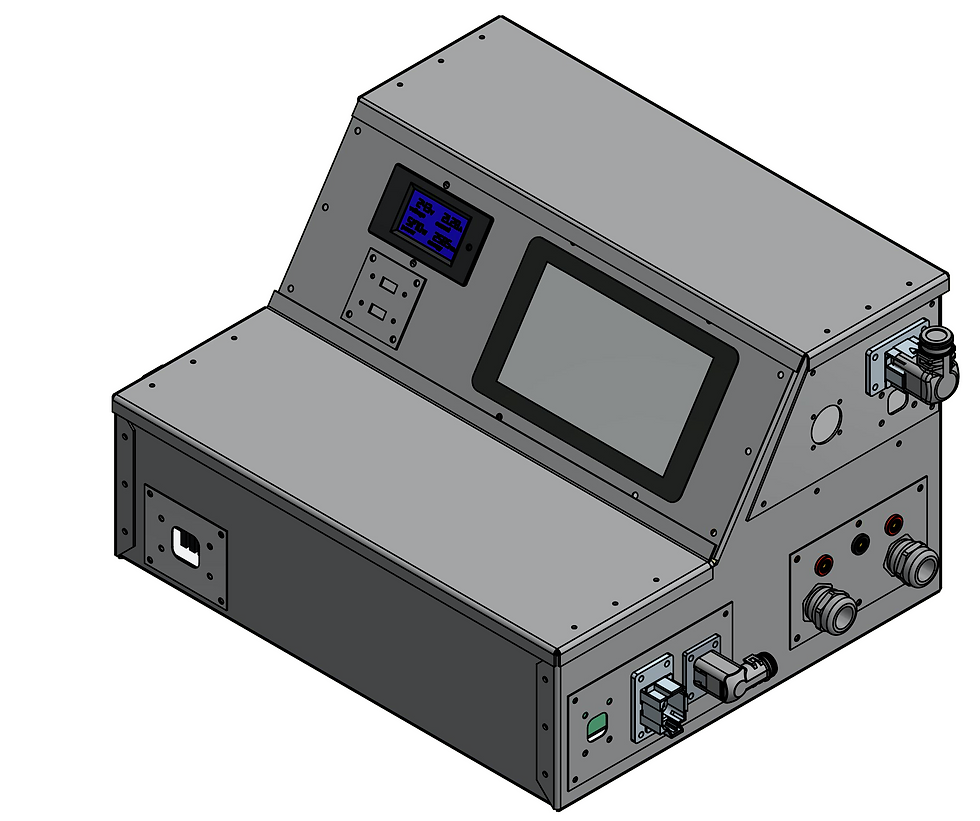
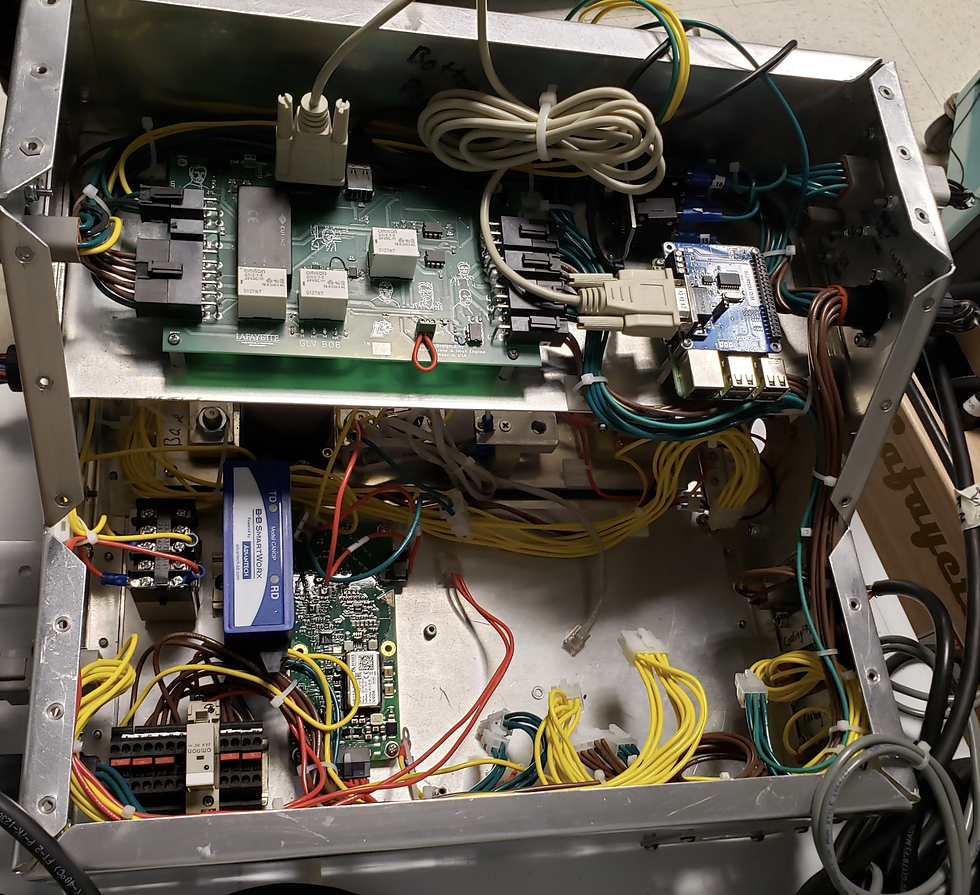
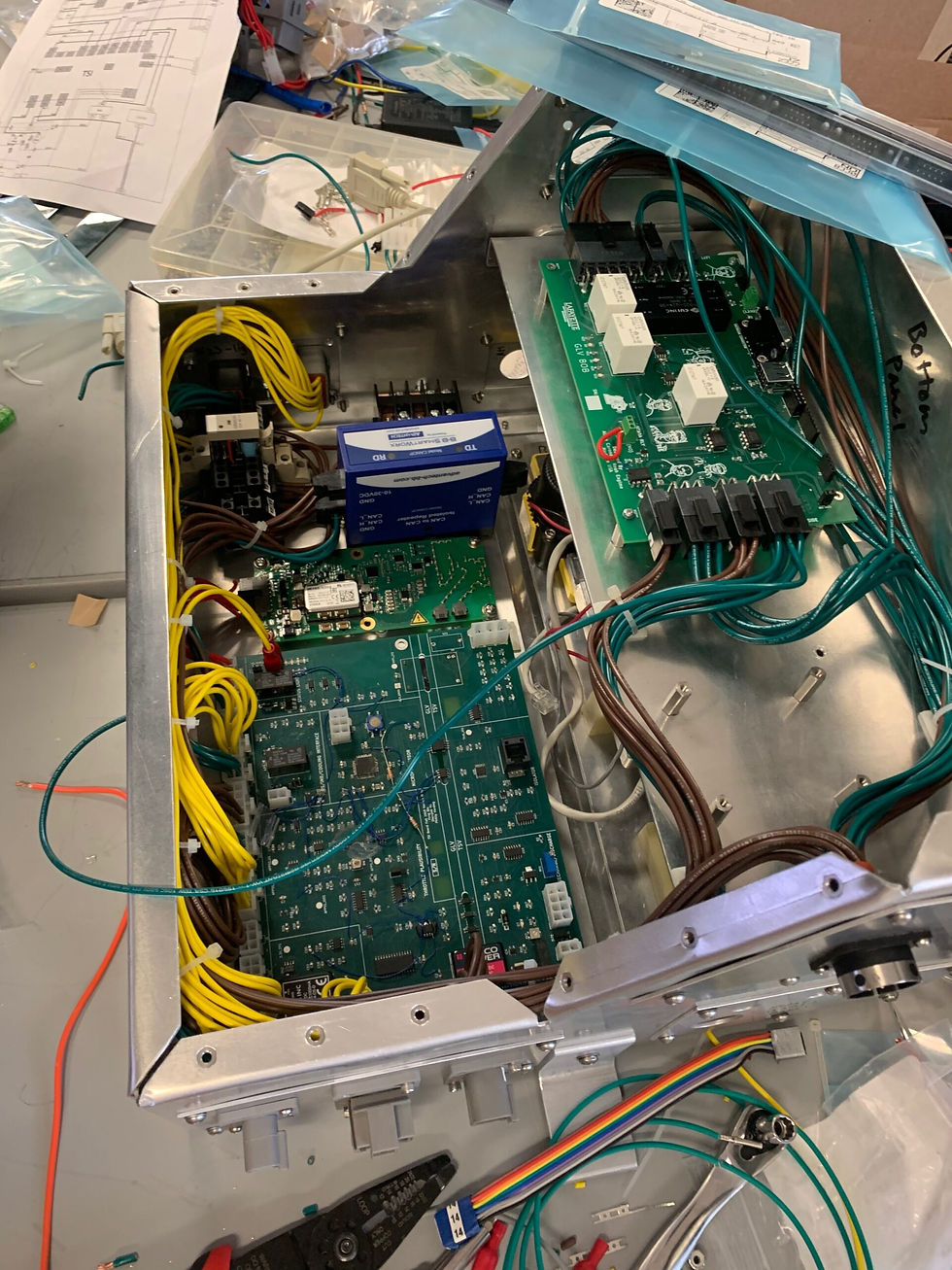
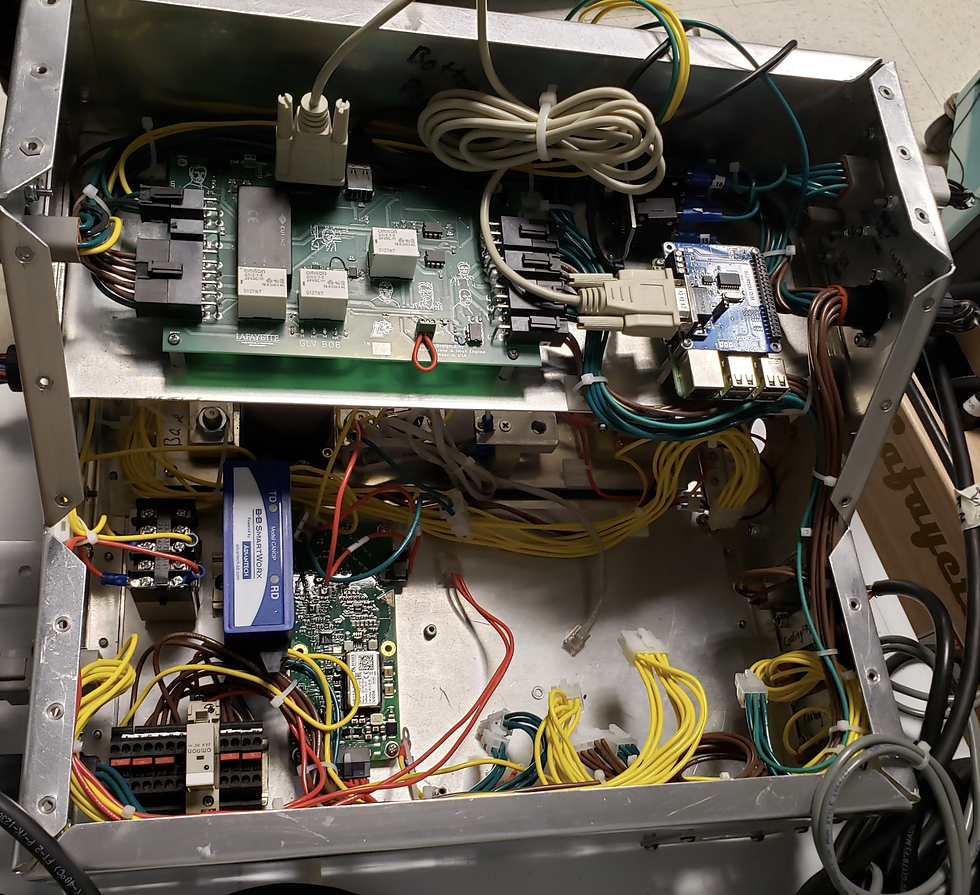
This project is the continuation of the test enclosure build. The following year I focused on designing on CarMan, a 'folded', compact version of the test enclosure.
​
Design Objectives:
-
FSAE rules compliance and strain relief
-
Cable organization and easy access to many electrical components
-
Low cost and easy fabrication
-
Water-resistant
-
Minimal use of loose fasteners
​
Design Features:
-
5 piece, riveted aluminum shell and an interlocking 3 piece lid allowing for access to each section of the enclosure
-
Low voltage shelf for GLV components
-
High voltage relay board
-
Mixed voltage tractive system interface
-
21 connectors/cables and 5 electrical boards
​
CarMan is the result of numerous design reviews and extensive collaboration between subteams.
Other Interconnect Team Projects

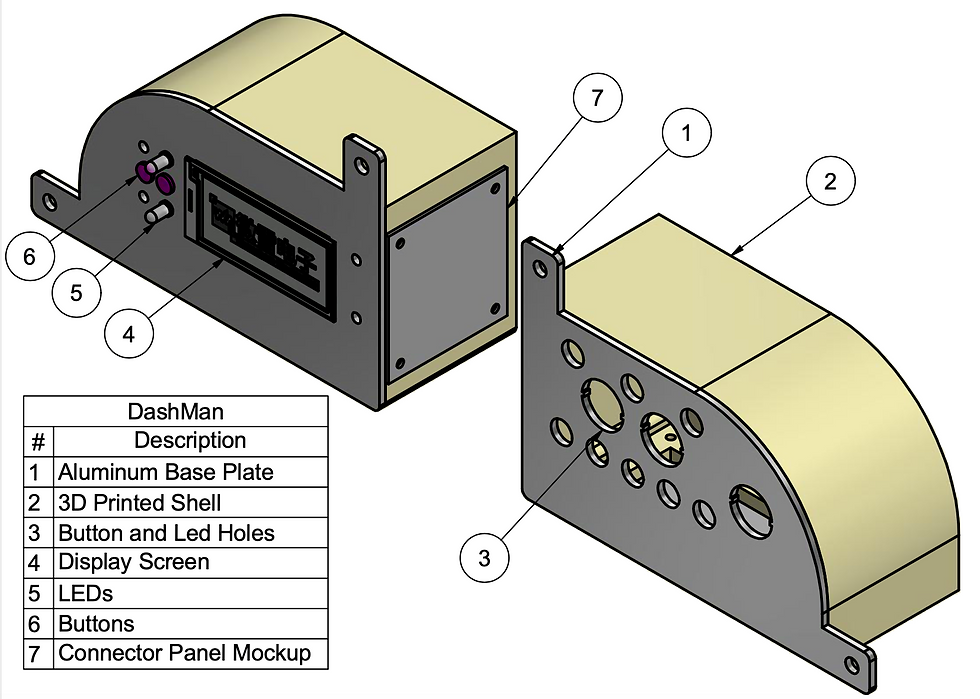
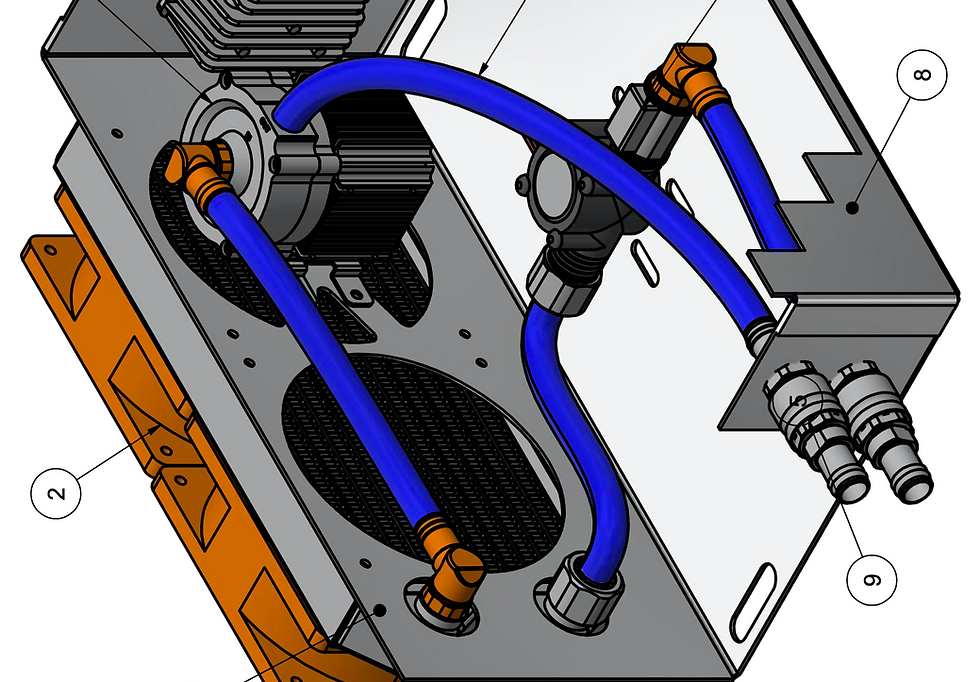

In addition to CarMan, I was also responsible for several other small projects:
-
Designed and fabricated a high voltage relay board. This is an iteration of my previous design
-
Designed a preliminary dashboard concept
-
Designed a cooling unit based on an existing test rig
​
​
Dynamometer Motor Mount
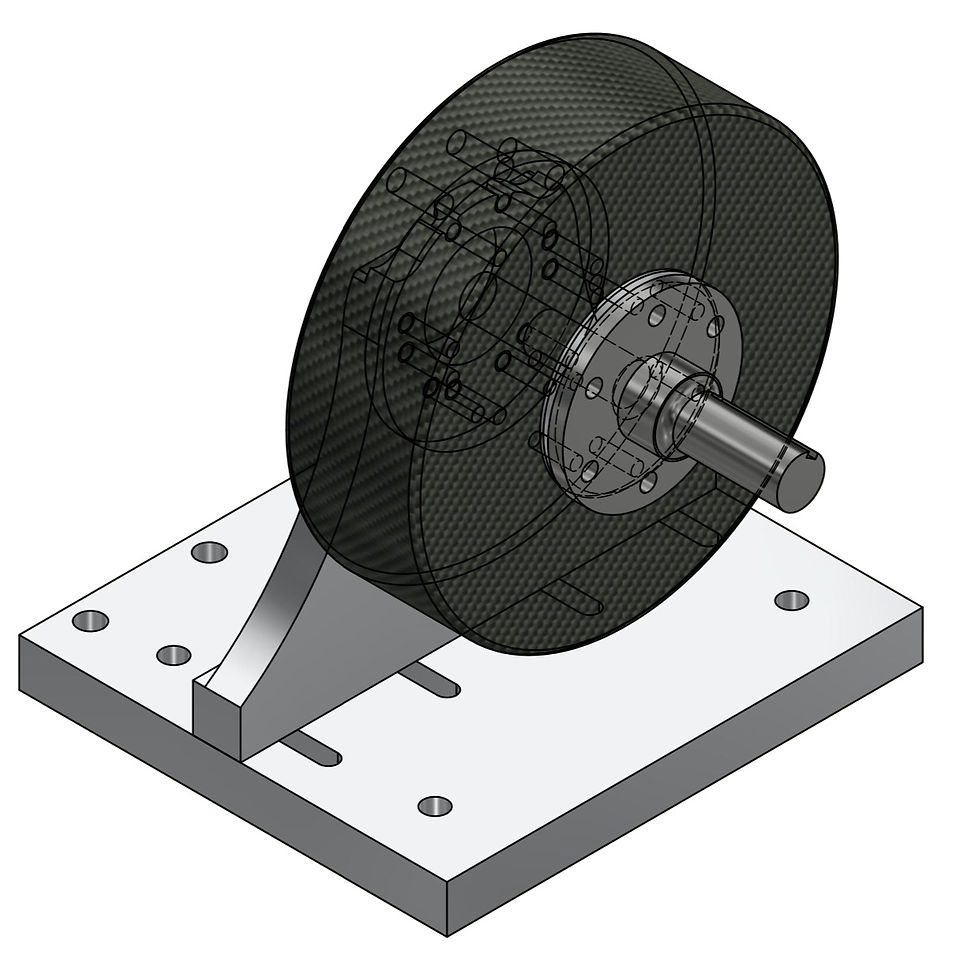
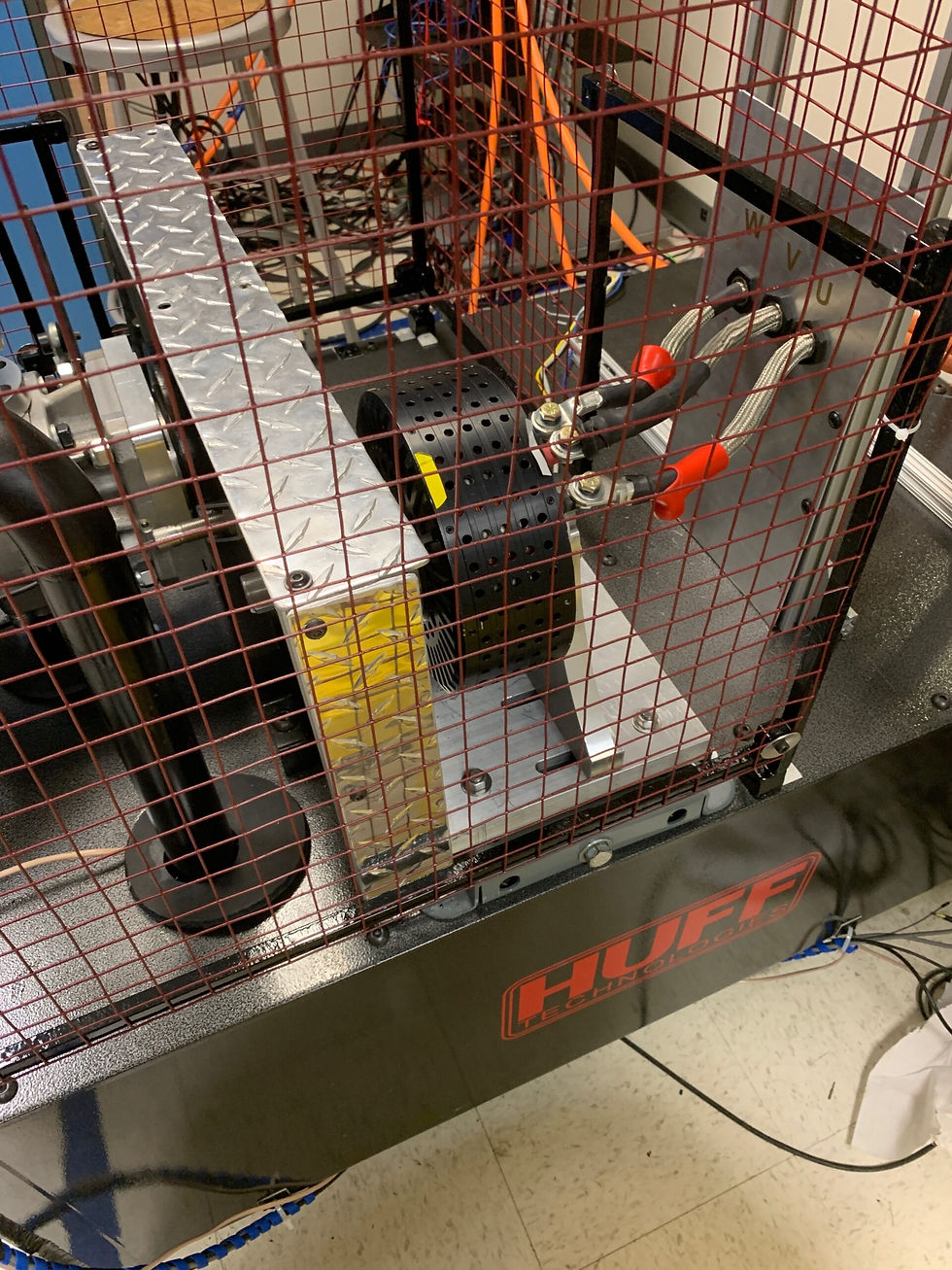

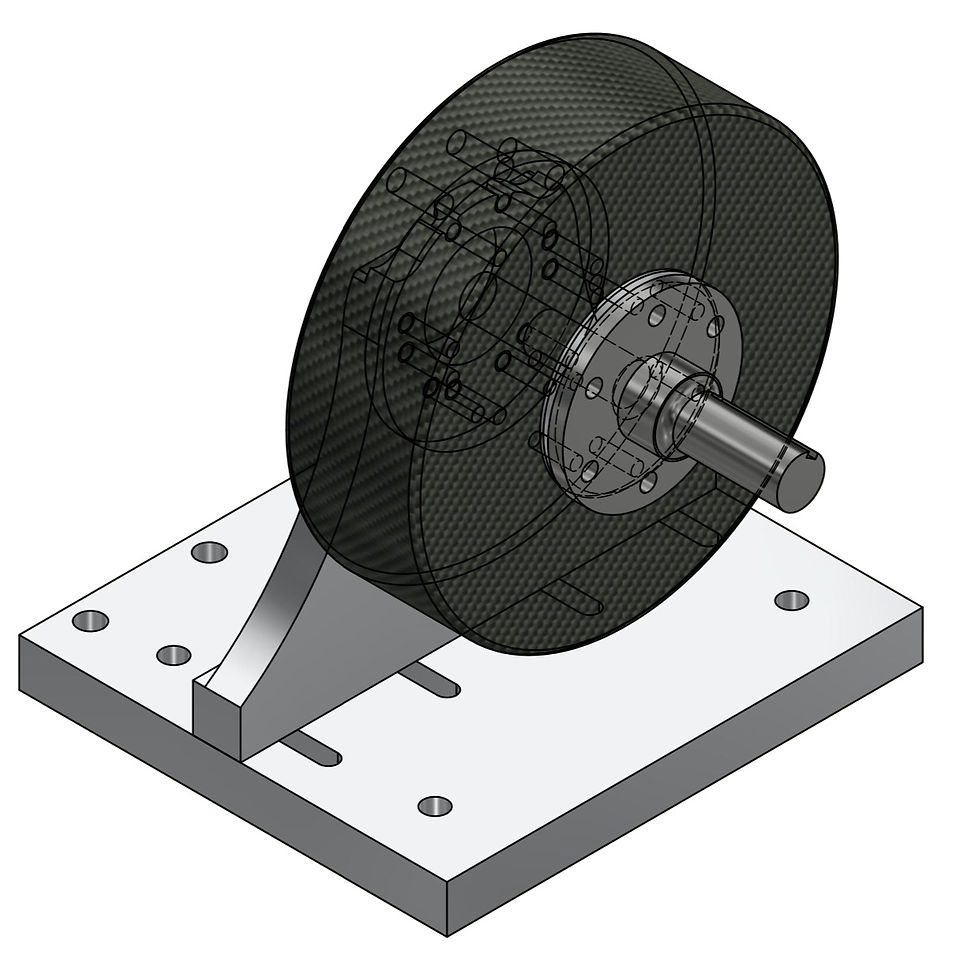
I volunteered to manufacture a mounting structure for an upgraded motor. This assembly consists of an Emrax 208 motor, mounting plate, and base plate.
​
Each part was designed in Inventor and manufactured using a CNC router.